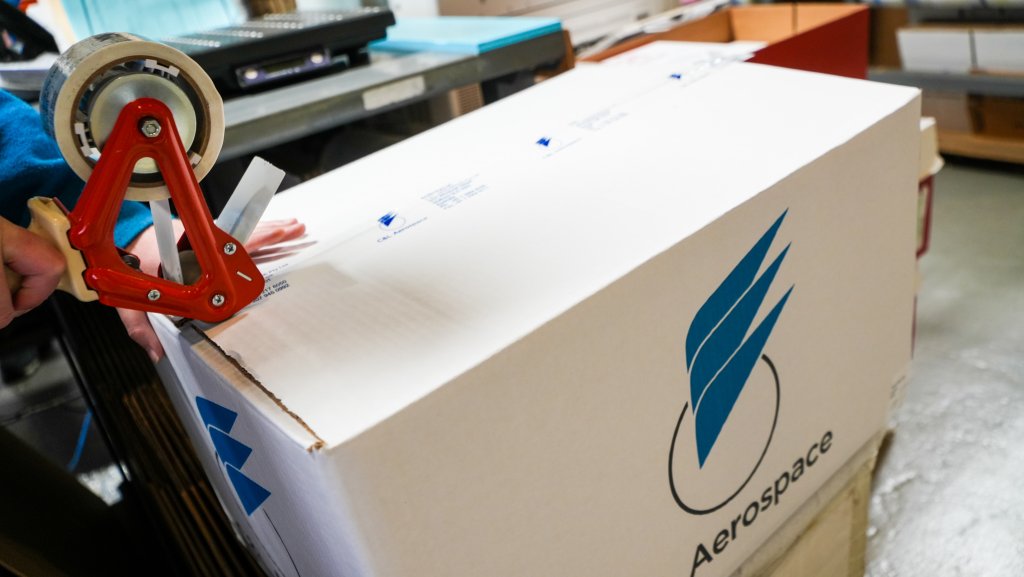
When you buy high-quality aircraft parts, you want them to be delivered in excellent condition. No one wants their aircraft part to arrive in a flimsy crate or unsuitable packing material. If the packaging is damaged, the part could be damaged as well.
What are Quality Parts?
At C&L Aviation Group, we believe that buyers should be able to see the aircraft part before making a purchase. “Quality parts” begin the moment an item enters the warehouse, whether by aircraft teardown, repairs, or intake of stock. It continues as each item is evaluated, photographed, and uploaded (with its appropriate documentation) to an aircraft parts database for buyer inspection.
What you see is what you should get. If the part is damaged during transit due to improper packaging, it is not a quality part anymore.
What are Our Packaging Standards?
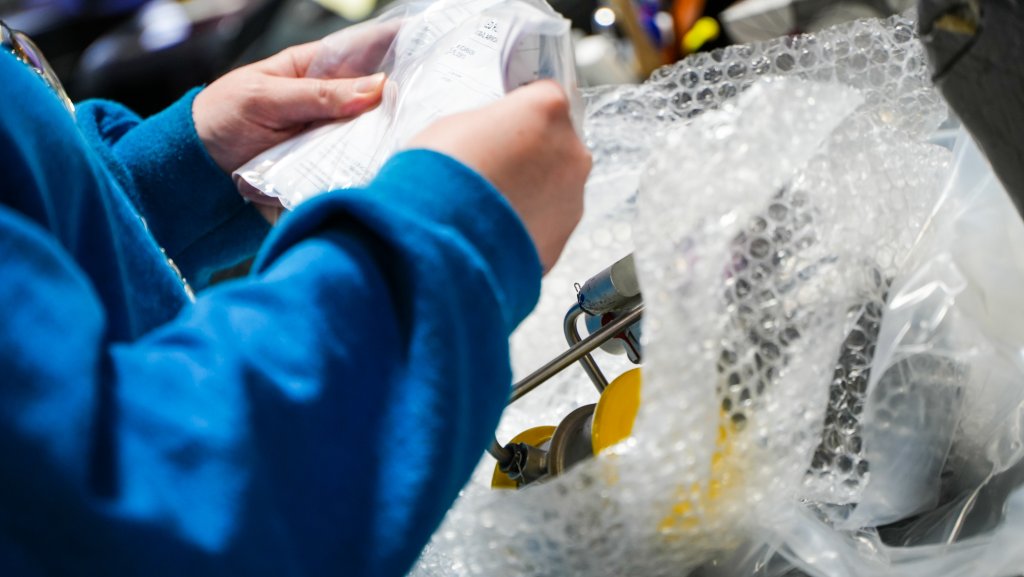
C&L’s Warehouse Specialists are responsible for packaging and shipping parts. The Specialists go through a detailed training process specifically designed to teach them how to pack items so that nothing reaches a customer in poor condition. The Specialists have a strict standard to uphold, as C&L sets a high bar.
Labels such as “Fragile” and “Handle with Care” are often overlooked by carriers (FedEx, UPS, etc.). Ensuring that a package is not damaged in transit starts with secure packaging, not just labels.
C&L’s packing philosophy starts with investing in good, sturdy wooden crates and fiberboard boxes. The Specialists start with top-quality crates and add braces and 2-inch foam padding (if necessary). This enhances the quality of the crate and ensures that nothing rubs, bumps, or moves within the crate.
Each item going out the door is evaluated according to which packing material – bubble wrap (electrostatic and regular), foam, plastic sealing, etc. – is needed to support a successful transport from Point A to Point B.
What if the Buyer has to Ship Back an Aircraft Part?

Sometimes an aircraft part is delivered that does not work or is no longer what the buyer needs and must be shipped back. If an aircraft part is purchased on exchange, a core will have to be shipped back. Buyers may not have the training of Warehouse Specialists, but there are a couple of options available to ensure that the part or core arrives safely.
If the buyer has the package the aircraft part was shipped in from the supplier, it can be used to return the part or to ship back the exchange core.
If the buyer no longer has the package, a new one will have to be obtained. Shipping a part with inadequate packaging may result in a billing for a replacement package.
No matter if you are the supplier or the buyer, having secure packaging matters.