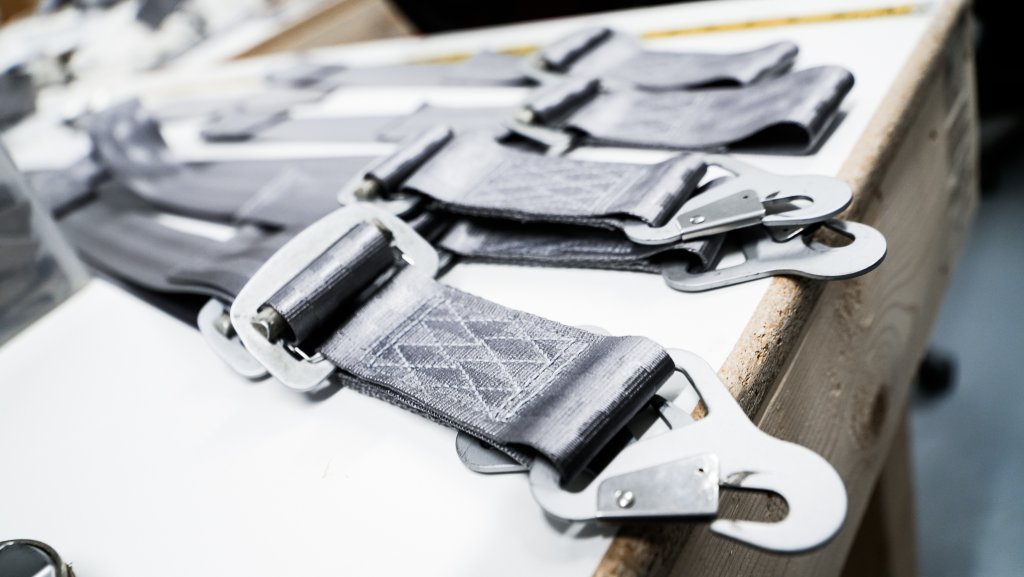
Aircraft seat belts play a critical role in passenger safety, and ensuring their integrity through regular re-webbing is a top priority for maintenance professionals. Here’s everything you need to know about preparing aircraft seat belts for re-webbing, including best practices for minimizing downtime and costs.
Why Re-Web Aircraft Seat Belts?
Aircraft seat belts generally require repair or re-webbing every 7 years. They should be removed earlier if the belts (also known as webbing) show signs of wear and tear or if the label is worn or torn.
Seat belts that are not functioning properly compromise safety – and ground revenue. Airlines and charter aircraft lose money on seats that cannot be sold to passengers due to faulty seat belts.
While old or damaged seat belts need to be removed and rewebbed to ensure passenger safety and prevent financial loss, there is another – more aesthetics-based – reason for re-webbing. Webbing color can be changed to complement the cabin, such as during seat reupholstery or interior refurbishment.
Pro Tip: Always consult seat belt labels or aircraft logbooks for your next inspection. The number of years between mandatory repair or re-webbing may vary depending on the seat or aircraft type.
What is Involved in Seat Belt Re-Webbing?
Re-webbing goes beyond swapping out old fabric. Not only is the webbing replaced, buckles and anchors are repaired or replaced if damaged; new labels are sewn onto the webbing; and an 8130 will be provided.
Seat belt labels specify the manufacture date, all part numbers, all subpart numbers, and the belt length. All repairs and new webbing must match the original part numbers and information on the old labels.
Pro Tip: Operators who want the seat belt length changed must contact the original equipment manufacturer (OEM) as this can only be accomplished as part of a modification.
What to Send to an Aircraft Seat Belt Repair Facility?
To ensure a smooth and cost-effective process, follow these best practices:
1. Send Complete Seat Belts
Repair vendors cannot accept seat belts that have been cut to shorter lengths, and they are not responsible for additional parts of the aircraft seat that may be removed along with the belts. These other parts must remain with the aircraft and risk getting lost if sent to another facility.
2. Send Legible Labels
Repair vendors rely on the information provided on the labels. If enough wording remains, a repair vendor may be able to replicate the belt accurately. If labels cannot be read or are missing, the seat belt will need to be sent to the OEM for replacement, which could be costly and time-consuming.
3. Send Additional Information (Optional)
Consider adding tags that identify which seat the belt was removed from as this is helpful for the repair vendor and the technician who reinstalls the belts. We recommend tying these tags to the buckles or anchors, rather than the webbing which will be replaced. Do not tape tags to the buckles as this could result in the plating being removed with the tape.
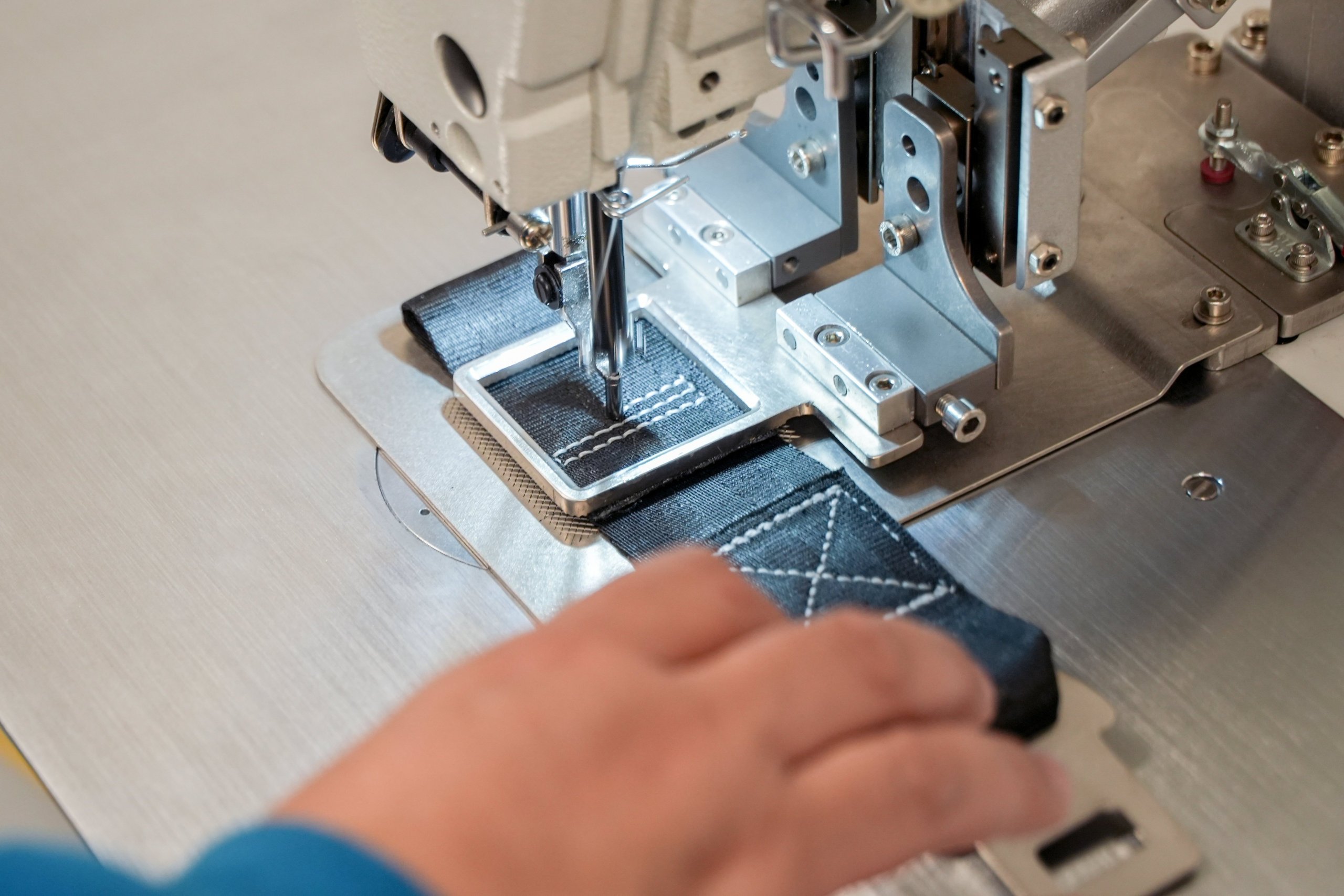
What to Communicate with an Aircraft Seat Belt Repair Vendor?
We recommend contacting the repair vendor before sending the aircraft seat belts. Here are some tips for open communication.
Prepare in Advance
Notify vendors of upcoming shipments so vendors can request necessary paperwork from the operator and acquire any custom materials, such as colored webbing.
Disclose Issues
Highlight any problems, such as faulty buckles or non-compliance concerns. Some issues can only be resolved through the OEM.
Ship Smart
Provide the vendor with the expected delivery date and any information the vendor requests. Vendors cannot work on seat belts without clear documentation about who sent them or what services are required.
Why Keep Rotable Seat Belts on Hand?
Keeping rotable seat belts available for immediate installation helps minimize downtime and loss of revenue. When a seat belt becomes faulty, you can replace it with an identical one, so you’re not left scrambling to replace or re-web it.
Final Takeaway
Our final piece of advice: Don’t wait. Be proactive and start the seat belt repair process whenever you notice seat belts with frayed webbing, illegible labels, or faulty components. It could save you from higher costs and longer repair times and elevate your passengers’ experience.