Retiring a regional or corporate jet can present challenges for operators who want to make the most of their investment. The good news is that even retired aircraft can still provide revenue in the parts market. Parts harvested from an aircraft teardown provide an important revenue stream and offer a sustainable and environmentally friendly solution to parts shortages.
Now, where do you begin?
As an aircraft disassembly partner, we know there are numerous factors to consider regarding an aircraft teardown, and we are here to help guide you through the process.
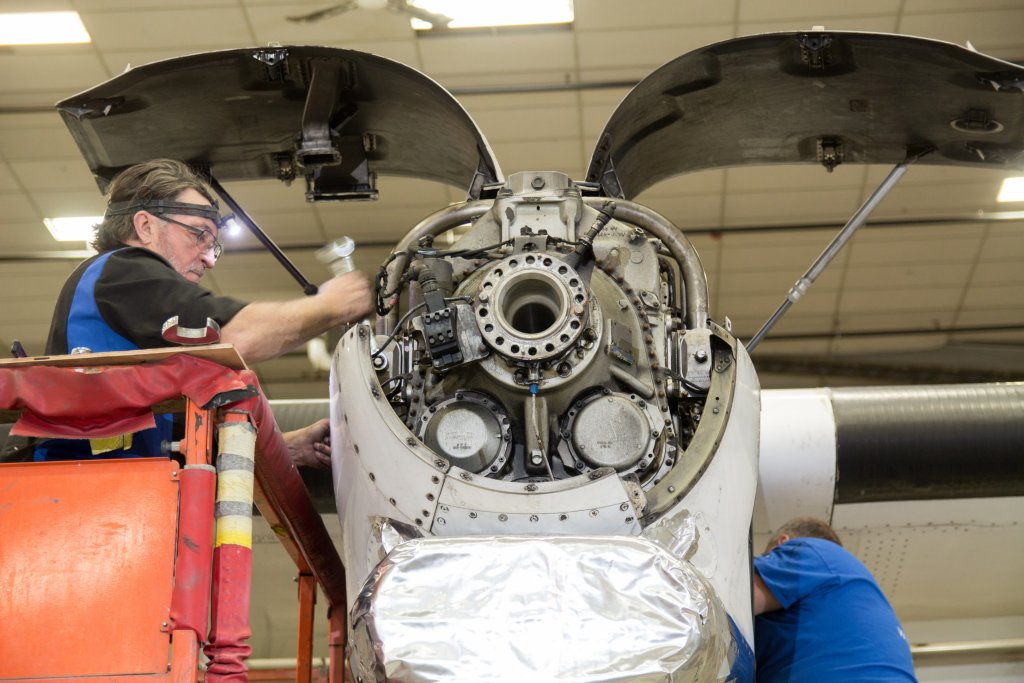
Why Part Out an Aircraft Rather Than Sell It?
If you are unable to attract a buyer for your aircraft, you might consider parting out the aircraft. While selling a retired aircraft is faster, the return on harvested spare parts may be higher, though not always. Be sure to do your research before making your decision.
Aircraft teardowns are long-term investments (generally 3 to 5 years) with more upfront costs in certification, freight, and storage. The upside, however, is that there is an active aftermarket for parts removed from retired aircraft. Plus, these parts may provide you with valuable spare parts to replenish your own inventory or sell on consignment to other operators.
What to Look For in an Aircraft Disassembly Partner?
When choosing an aircraft teardown partner, always check reviews and ask for references to ensure their capabilities. Important considerations in choosing a partner are that they have performed many of these teardowns previously, can travel anywhere in the world to perform a teardown, and have the sales network to be able to sell the parts as quickly as possible.
Why Choose a Consignment Partner?
If you are selling parts, consider working with an aircraft disassembly partner who can assist with facets of the process. Having the infrastructure already in place to be able to sell the parts on your behalf is an important piece of this process. Services available through a consignment partner may include aircraft teardown, logistics for moving parts and/or aircraft, warehouse storage, repair management, marketing, sales, and shipping. Generally, you will receive a regular payment for parts sold each month.
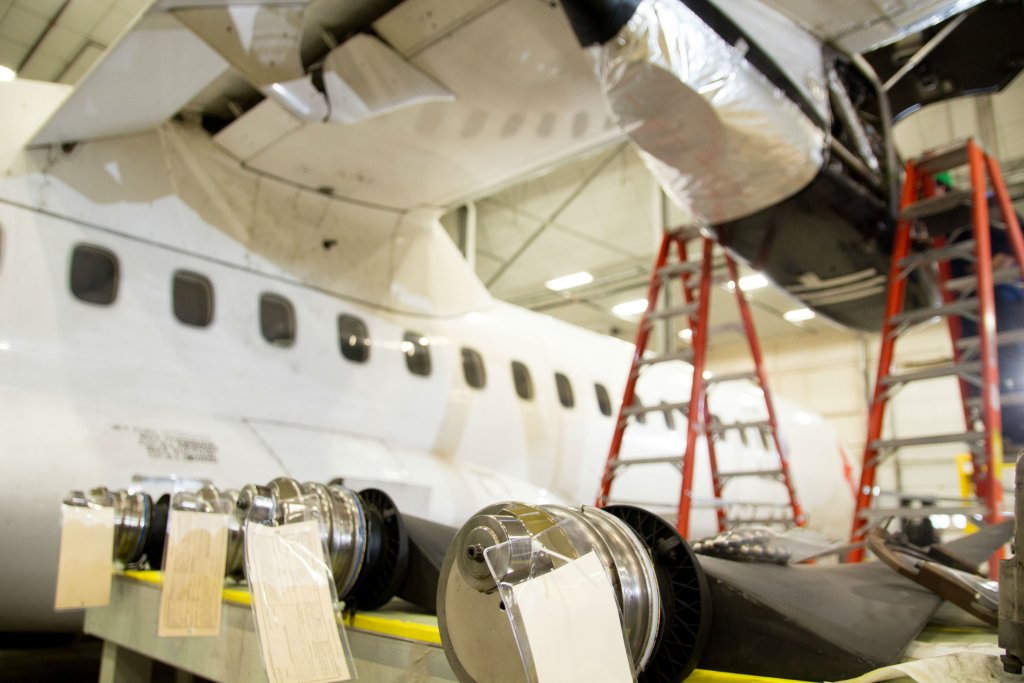
How Much Do Aircraft Teardowns Cost?
Regional and corporate aircraft teardowns typically cost between $60,000 and $100,000. These costs cover disassembling the aircraft, disposing of unusable or hazardous material, identifying and tagging each part, packaging, crating, and loading for transport. Costs can vary depending on the location of the teardown in terms of labor costs and logistics (i.e., freight costs).
How Long Do Aircraft Teardowns Take?
Most aircraft teardowns take approximately 3 to 6 weeks.
Does Location Affect the Aircraft Teardown Process?
The teardown location and time of year are important to consider. Both can impact how quickly and conveniently the teardown process is completed. Operators should choose a location where the aircraft can be easily delivered (by flight or transport) and where harvested parts can be easily shipped to the operator’s facility or repair vendor. Operators should consider shipping options, freight costs, and clearing customs, if applicable. Also, depending on the facilities at the teardown site, consider adverse seasonal weather. The weather could prolong the teardown process during certain times of the year.
What If You Can’t Fly to an Aircraft Teardown Facility?
If the aircraft is inoperable or cannot be transported to a disassembly facility, a teardown partner can travel to the aircraft’s location.
What Aircraft Parts to Include on a Harvest List?
A harvest list specifies the aircraft parts operators wish to acquire from a teardown. The list generally consists of high-value parts (i.e., engines, landing gear, avionics, windshields, etc.), high-use parts, and rotables.
Typically, harvest lists include 600 to 1,000 parts. Although aircraft consist of considerably more parts, it is unlikely that you will need to acquire them all. You’ll only need the ones that best meet your needs or will get a high return on the market.
What to Know About Engines During Aircraft Teardowns?
Engines are one of the first parts to be removed from the aircraft during a teardown and are the highest-valued parts on the aircraft. Engines can be sold, leased, or further torn down for engine part spares to be used at other engine shop visits. Removing the engines requires qualified technicians and specialized tools – more so than other parts. Engines will also require proper tooling and specialized shipping containers to ensure they are not damaged.
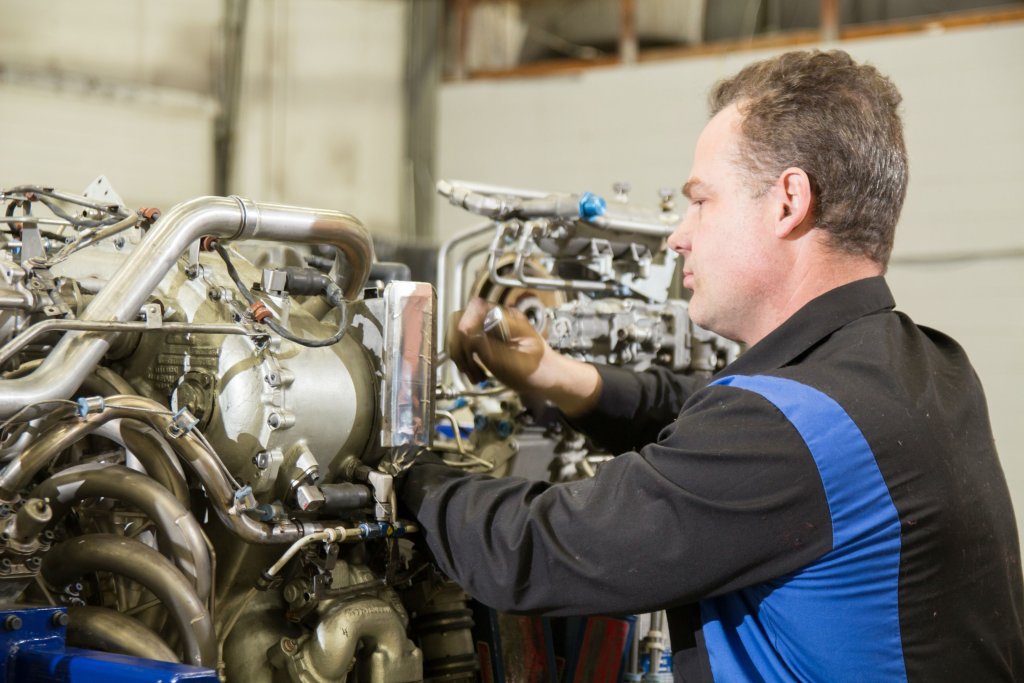
What to Expect During an Aircraft Teardown?
Once an aircraft arrives at the disassembly facility (or a disassembly team goes to the aircraft), the liveries are painted over and major aircraft parts, such as engines and auxiliary power units (APUs), are removed. Then, parts from the operator’s harvest list are set aside and tagged “as removed” (AR). Other important information is recorded, including the serial number of the aircraft, TSN (time since new), and CSN (cycles since new) of the aircraft, and removal date. Generally, all removed parts should be inspected, repaired, or overhauled as necessary before installation on another aircraft. Finally, the disassembly partner recycles and properly disposes of any aircraft parts not specified by the harvest list.