Trace documentation may be required when purchasing or transferring an aircraft part. Trace provides information about a part’s history, but the type of information provided varies depending on the situation. For this reason, knowing what trace documentation is and when it may be required can be confusing. To alleviate confusion, we compiled this article to explain what you need to know about aircraft part trace documentation.
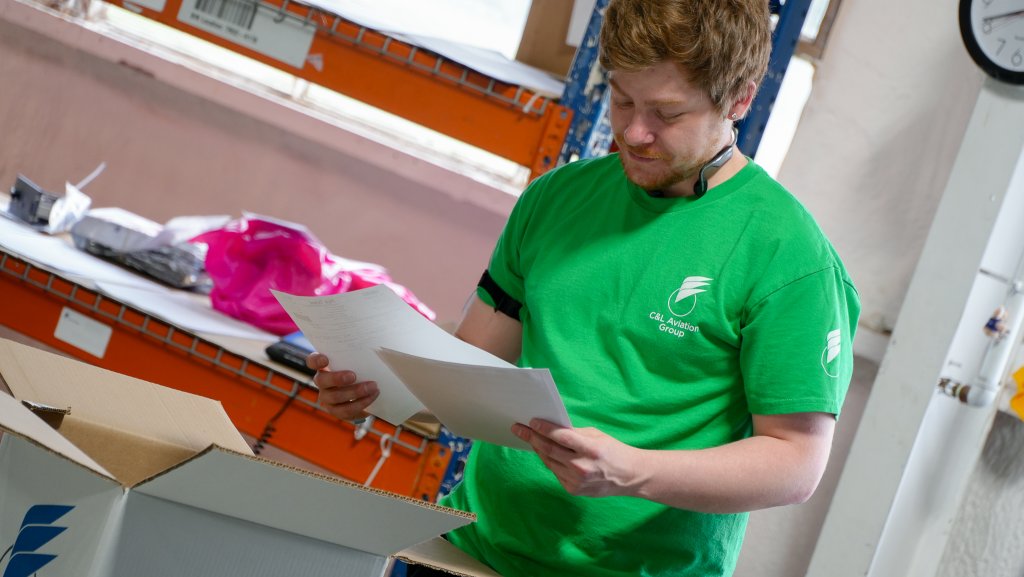
What is Aircraft Part Traceability?
Buyers and suppliers may rely on aircraft part traceability to understand the part’s history, which could go back to the previous operator or original manufacturer. Trace documentation may be requested to meet regulatory or operator requirements to ensure trust and the transfer of validated data about an aircraft part between a supplier and buyer.
Aircraft Part Trace Documents
Various documents can contain aircraft part trace information and each document varies in the amount of trace information provided.
ATA Specification 106 Form
An ATA Specification 106 Form (often shortened to ATA 106 or Spec 106) is a standardized industry form that provides aircraft part trace information to the previous source. It is commonly used to ensure quality assurance and includes a non-incident statement.
Non-Incident Statements
A non-incident statement (NIS) is a letter confirming that the aircraft part was not removed from an aircraft involved in an incident or accident. The NIS also states that the part was not subjected to severe stress or heat or immersed in salt water. It also confirms that the part was not removed from a military aircraft.
Other Types of Trace Documentation
Invoices, packing lists, part warranties, bills of sale, and other transactional documents can be used for aircraft part traceability. These forms of documentation typically include the part number (PN) and serial number (SN) of the aircraft part, manufacturer details, production date, and relevant certifications or test reports that help to demonstrate a direct link between previous and current owners, just like the ATA 106 Form.
Back to Birth Traceability
Back to birth (B2B or BtB) trace requires various forms of documentation to compile the part’s complete history. This may include but is not limited to the following:
- manufacturer certification,
- original log cards,
- build specifications,
- previous operators’ removal or installation documentation,
- maintenance documentation, and
- any statements from prior operators.
BtB provides unbroken or complete trace documentation. This shows the aircraft part’s times and cycles, installation, removal, and repair history from when it was first manufactured. BtB traceability is commonly used to track the calendar, time, or cycles of life-limited parts (LLPs) for engines, APUs, starter generators, etc.
When is Aircraft Part Trace Documentation Required?
Trace documentation may be required for different reasons. Below is a list of when certain forms of trace documentation are usually used.
- ATA 106 Form and NIS – These forms of trace documentation are required for all rotable aircraft parts during a transaction to provide information about the part back to the previous operator.
- BtB and Unbroken Trace – These forms of trace documentation are always required for LLPs or if a subassembly has LLPs installed. LLPs require documentation that outlines the entire life of the part.
How to Acquire Aircraft Part Trace Documentation
While some documents, such as invoices or packing lists, may be available, more extensive documentation might need to be acquired. Trace documents can be obtained from the previous supplier or operator. Suppliers generally maintain records for a few years after a part has been sold.
Aircraft Part Traceability Advice
Aircraft part traceability helps to ensure parts have not been involved in an incident or accident, or removed from a government or military source. However, by themselves, trace documents do not guarantee the credibility of a part. Verifying that trace documentation comes from a reputable source, which can be achieved by researching the supplier, is considered good practice to ensure the part’s legitimacy.