Have you been considering a repair management solution for your CT7 engine? Aircraft engines are a major investment, and a repair program can be an effective and economical way to receive service and procure parts when they are needed the most.
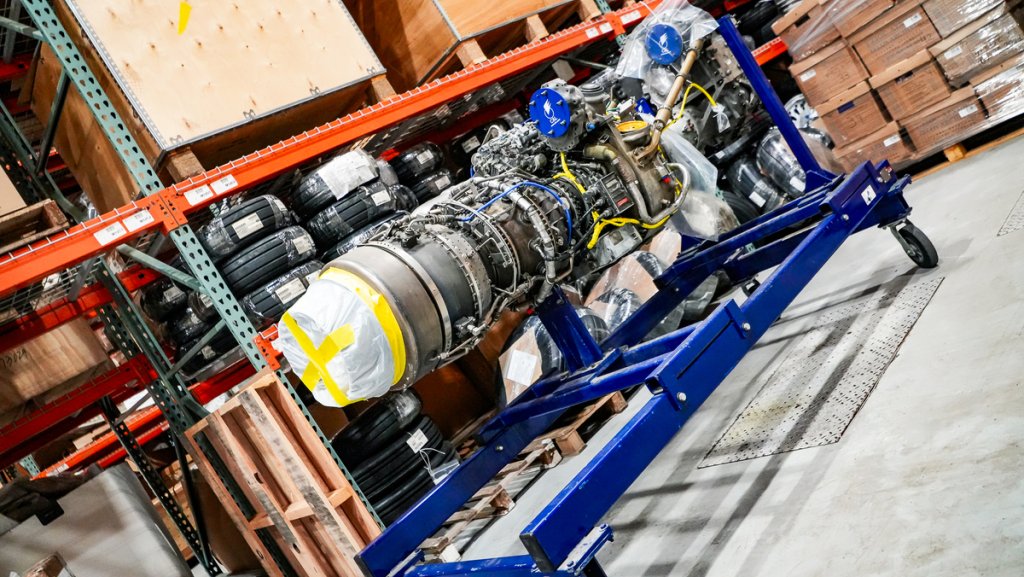
We’ve been supporting CT7 engines for years, and in this article, we share what CT7 repair management is, what factors impact costs, and how long engine repair takes to help you understand the program’s benefits.
What is CT7 Repair Management?
CT7 repair management covers the entire repair process for the full engine or the individual modules. The repair process is managed by a provider who completes the following tasks:
- Assessing the reason for repair and determining an adequate work scope with the customer
- Sending the engine or module(s) to a CT7-approved repair vendor, contingent upon the operator’s approval of the work scope
- Managing pre- and post-shipment tasks to and from an approved repair vendor, such as documentation, shipping, and other logistics
- Procuring difficult-to-obtain parts or components, such as line replaceable units (LRUs)
How Often Do CT7 Engines Need Repair?
The CT7 is a modular engine design permitting on-condition, individual module repair. Each engine consists of multiple modules and depending on the work required, a single module can be repaired, rather than the entire engine. A provider may be able to replace a removed module with another one, returning the engine to service more quickly than waiting for the module to be repaired.
Various factors contribute to the CT7 repair scope, frequently including but not limited to:
- The operating environment (e.g., a salty or corrosive atmosphere, etc.)
- Engine operation (e.g., proper CTOT (calculated take off time) use instead of excessive torque and temperature limits during takeoff)
- High-cycle operations
Why Choose a CT7 Repair Management Solution?
The primary benefits of choosing a CT7 repair management solution include cost savings, reduced turnaround time (TAT), and part availability from readily accessible inventory, all of which contributes to a more cost effective and timely shop visit.
Given current supply chain challenges, now is a great time to consider a CT7 repair management solution, especially for operators not currently on a program.
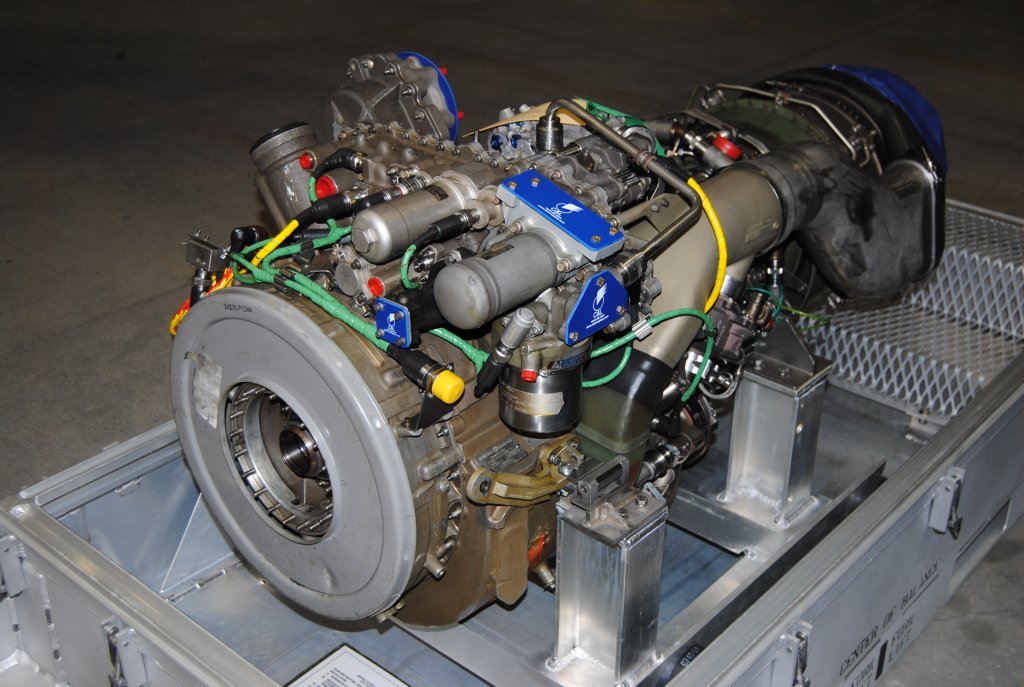
CT7 Repair Management: Factors for Cost
CT7 repair management can be more economical. However, cost saving opportunities will vary for every repair situation. The extent of these savings depends on but is not limited to the following factors:
- The scope of the repair project
- The amount of time since the last repair
- Current service bulletin (SB) application
- Replacement part availability
In certain situations, the age of the engine or the frequency of its use can also influence repair costs.
CT7 Engine Repair Management: Timeframe Factors
Under ideal circumstances, engine repair takes approximately 150 days. However, this timeframe can vary based on:
- The repair shop’s current workload
- Potential supply chain issues
- The time required for the operator to approve the work scope
CT7 Engine Repair: Concluding Thoughts
Opting for a CT7 repair management solution can lead to significant operational benefits, including the management of the entire process, part procurement, cost savings, reduced turnaround time, and the possible availability of an exchange engine. By understanding the process and factors, you can determine whether a CT7 repair management solution is the right choice for your operational needs.