Understanding aircraft part conditions is important to the sales process and your satisfaction – is the aircraft part fresh from the manufacturer or quickly approaching the scrapyard? This article provides you with definitions for 10 aircraft part conditions and their abbreviations. We also provide tips for making informed aircraft part sales decisions.
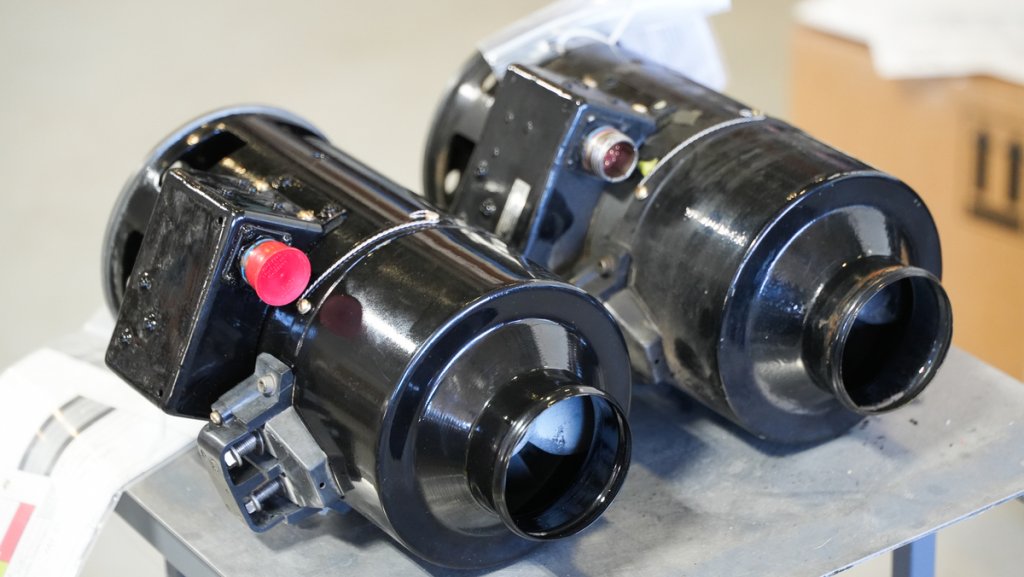
What are the 10 Aircraft Part Conditions?
The following list of part condition abbreviations or codes is ordered from (approximately) the most expensive to the least.
1. Factory New (FN)
Aircraft parts in FN condition are brand new from the Original Equipment Manufacturer (OEM), i.e., no more than 2 years from the manufacture date. The aircraft parts should come with the manufacturer’s certificate of conformance and could also have an 8130, depending on the type of part. FN parts should not have any operating time or cycles and have not previously been installed on an aircraft.
2. New (NE)
New aircraft parts have never been used and have no operating time or cycles. Although they may not have come directly from the OEM, new parts should still retain OEM certificates and all necessary trace information.
3. New Surplus (NS)
New Surplus aircraft parts have usually gone through one or more sellers but have never been used and have no operating time or cycles. Some NS parts may not have the original certification paperwork from the OEM. They may, however, have a certification of conformance and trace documentation from the seller.
4. Modified (MD)
A modified aircraft part has been altered in some way from its prior configuration. This can happen during a repair or overhaul. The teardown report outlines what modifications were made. Alterations could be as simple as a software upgrade or as complex as a structural modification.
5. Overhauled (OH)
Aircraft parts in overhauled condition have been refurbished following the applicable standards, such as the part’s Component Maintenance Manual (CMM). Overhauled parts cost less than new even though they are considered the most premium condition for used aircraft parts on the market.
6. Serviceable (SV)
Aviation parts in serviceable condition have been inspected and deemed airworthy and ready for return to service. If you are considering a serviceable part, you should review the part’s certification and accompanying inspection report to confirm details of the part’s condition. Serviceable parts fall into one of three subcategories: repaired, tested/inspected, or visually inspected.
6.1. Repaired (REP)
A repaired aircraft part was previously faulty or in need of some refurbishment. This part has been restored to airworthy condition through an appropriate FAA (or equivalent) approved repair process. The details of this repair should be listed on the teardown report associated with the release of the service tag (either an 8130 or other maintenance release tag).
6.2. Function Tested (FT) or Tested or Inspected
Tested aircraft parts have gone through a required inspection/evaluation process to prove they are functional. If the parts pass the approved testing procedure, they will be certified and put back into service. A few scenarios in which parts may require testing include:
- The part may have a mandated, incremental test (e.g., Challenger 604/605 Flutter Dampers require a functional test every 4,800 hours of operation).
- The part has been out of operation for a long time. It may have to be inspected to ensure serviceability before being installed on an aircraft.
- The part was removed from a working aircraft or an aircraft that is being torn down for parts. In the latter situation, the part may not require a repair but rather pass a simple bench check or inspection before being put back into service.
6.3. Visually Inspected (IN)
Aircraft parts that are certified as “Visually Inspected” indicate that the part received a general visual inspection after removal from an aircraft to determine serviceability.
7. As Removed (AR)
As Removed parts are in the same condition they were when taken from an aircraft. They have not been inspected or tested. AR parts may be removed from a fully-operational aircraft during teardown to be resold or because they were faulty and were used as a core through an exchange.
AR parts do not include an airworthiness certification. (If certification is required, the buyer could arrange for the part to be evaluated and certified through an approved repair shop.)
8. Rejected (RJ)
There are several reasons why a part may have been rejected by its last user or repair shop. In some cases, the part may be rejected because the part is unrepairable or the repair cost is not economical.
9. Beyond Economical Repair (BER)
A part may be deemed Beyond Economical Repair for one of two reasons. First, the cost to repair or overhaul may exceed the part’s value. Second, the replacement components necessary for repairing or overhauling the part may no longer be available.
10. Rebuilt (RB)
Rebuilt is a used aircraft part that has been completely disassembled, inspected, repaired as necessary, reassembled, tested, and approved in the same manner and to the same tolerances and limits as a new part. It may be repaired with either new or used components. All rebuilt parts must conform to the production drawing tolerances and limits for new parts.
What Part Conditions Can Be Used on Your Aircraft?
Before buying a part in any condition, you need to know if that part condition is acceptable on your aircraft. Your organization may have stipulations or quality standards that inform which part conditions are allowed for installation on your aircraft.
You must review your organization’s quality standards to see what part conditions are considered acceptable for your specific aircraft.
Tips for Purchasing Aircraft Parts Based on Part Conditions
Once you know what part condition to obtain based on your organization’s quality standards, you can prepare for the purchase. The following are a few things to keep in mind.
Budget
Having a budget allows you to allocate the necessary funds for obtaining the part you need in the condition you want. A detailed cost estimate for aircraft maintenance can help you anticipate when parts need to be purchased and how to budget.
Research and Part Availability
Any advanced research on available aircraft part options will help you throughout the procurement process – especially when looking for possible upgrades or alternate parts. This research can introduce you to other options that are available in the market that suit your needs.
It never hurts to ask your part supplier about alternatives and upgrades.
Timeframe for Purchasing
If the part you need is not available in the condition you want, you may be able to wait for the part to become available. Alternatively, you could have a part in lesser condition repaired or overhauled to the condition you need.
If you do not have time to wait, you may have to choose the next best option, even if it is a lesser condition. (Be sure to confirm that this condition is still acceptable per your organization’s standards.)
Lead Time
Also, you should account for a supplier’s delivery or lead time. If the part is in stock, it should be available for immediate shipment. Other lead times might range from a few days to several months. This may depend on whether the supplier is obtaining the part directly from a manufacturer or if the part is in the process of being repaired or overhauled.
Warranties
Aircraft part warranties may also factor into your purchasing decisions because different part conditions have different warranties. Reviewing the seller’s warranty and return policies before committing to a purchase is the best practice.
Make Sure You Get the Aircraft Part Condition You Paid For
Our advice is to always request copies of certification and photos of aviation parts from your supplier. This helps to ensure you are obtaining the part in the condition you specified.
No matter the part condition, you should review any documentation that accompanies the part. By reviewing certifications, trace documents, teardown or inspection records, or any other applicable documentation, you will gain insight into the part’s true condition and history.
The part should look like it is in the condition you want, and it should have the appropriate documentation to confirm its condition.