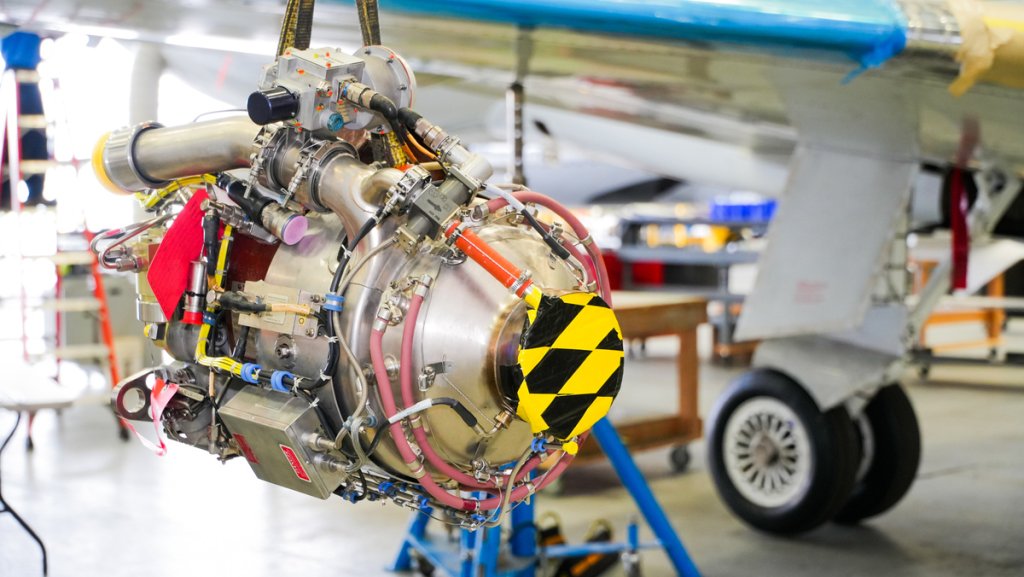
Have you ever considered how difficult it is to ship an aircraft engine or APU? We mean, really thought about it?
Aircraft engines and auxiliary power units (APUs) are major investments. If not properly packaged and shipped, these aircraft parts could be damaged during transit, resulting in higher repair costs and prolonged downtimes. So, why take that risk?
We’ve been shipping and receiving engines and APUs for years, and we’ve seen everything from carefully mounted engines to units thrown into a crate on a bed of trash and desiccant bags wrapped in plastic. We decided it was high time we addressed this inconsistency and helped our customers discover best practices for shipping these high-value aircraft parts.
How to Prepare an Aircraft Engine or APU for Shipment
An aircraft engine or APU may be shipped for various reasons. For instance, the part could be shipped to a new owner or repair vendor. It could also be sent to a supplier as a core during an exchange transaction.
Before shipping the engine or APU, it should be drained and/or purged of any hazardous materials. If it contains hazardous fluids, such as engine oil, it will be considered a dangerous good (DG). As such, it is subject to D.O.T. HAZMAT regulations and will be significantly more costly. (See Purge Certificate below.)
How to Package an Aircraft Engine or APU
Regardless of the reason for shipment, engines and APUs should be carefully and properly packaged.
Engine/APU Mounts and Containers
Aircraft engines and APUs are usually bolted onto special mounts and placed inside a shipping crate or container. These mounts suspend the engine or APU, protecting it from shock if the container is jostled or dropped. To further mitigate damage, engine mounts include shock absorption pads between the mount and the engine or APU frame.
It is considered best practice to use an OEM-approved mount and container specially designed for the engine or APU. They can be acquired from the supplier or engine manufacturer. If you are returning a core, you can ship the engine or APU using the same mount and container the exchange unit arrived in.
Packing Material and Humidity Indicators
Once the engine or APU is bolted to the mount, it should be wrapped in plastic, and vacuum sealed in some cases, so it is air-tight. A humidity indicator and desiccant packets should be placed in and around the plastic-wrapped part to eliminate the threat of moisture. Moisture can corrosion and potentially damage internal components.
Some humidity indicators change color, such as from blue to pink, to demonstrate whether the crate contains at least 30% moisture. If moisture is present, desiccant packets should be replaced with fresh ones. (Note: Desiccant packets should be removed from plastic bags before being placed in the shipping container as plastic bags can hinder the packets’ ability to absorb moisture.)
Refer to the engine’s or APU’s component maintenance manual (CMM) for packing and shipping instructions.
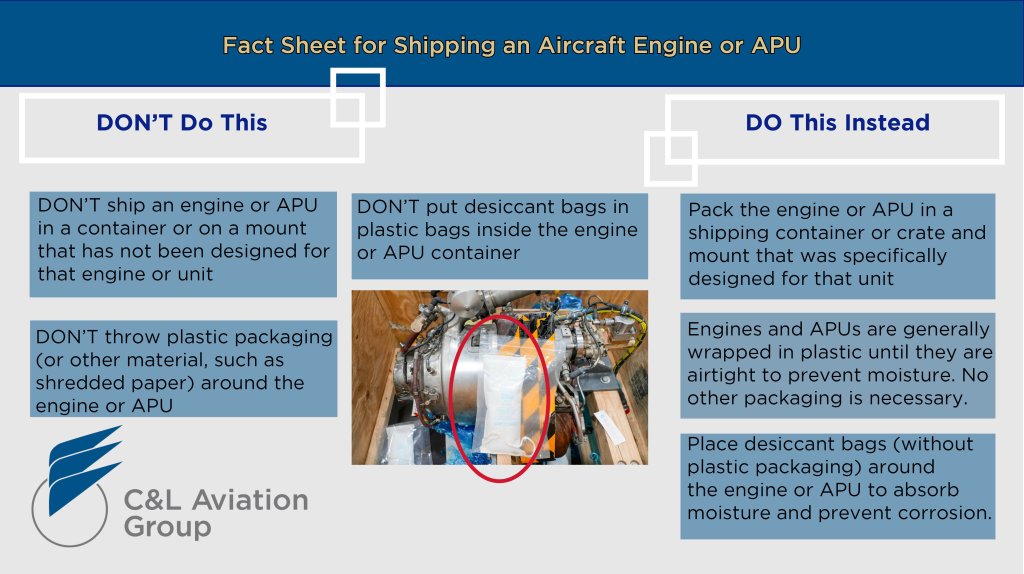
Shock Indicators
If the part is properly mounted, it shouldn’t move inside the shipping container or require extra packing. Sticker indicators should be placed on the container to show if it experienced rough handling, potentially damaging the part inside.
A ShockWatch® turns red if the engine experiences extreme force, generally more than 25 G-force. A Tip N Tell® indicator reveals if the container has been tipped onto its side via a triangular space that fills with liquid if tilted.
Transportation Considerations
When packaging an engine or APU for shipment, it is important to consider transportation. For ground transportation, opting for a truck with air-ride suspension to mitigate shock and bumps is generally a wise idea.
What Documentation to Include with Shipment
Logbooks
Aircraft engine and APU logbooks generally must be available with the shipment. The logbooks may be included with the shipment or sent to another department, depending on the company’s policy.
Logbooks provide all trace information about the part back to birth. This information generally includes, but is not limited to, the time since new or overhauled (TSN or TSO) or cycles since new or overhauled (CSN) or (CSO), service bulletins (SBs), airworthiness directives (ADs), and subcomponent installation. Plus, it lists all shop visits and when the part was installed and removed from an aircraft. The logbook must include the most recent removal date, along with the TSN and CSN at the time of removal.
Suppliers or repair vendors might not accept the engine or APU if trace documentation is missing.
Shipping Information
Engines and APUs require the same shipping information and paperwork as other aircraft part shipments. The engine or APU shipment needs a specific transport document depending on how the shipment will be transported. For instance, an air waybill is used for air freight and a bill of lading (BOL) is for sea freight. A commercial invoice is required if the part is being shipped internationally. These are legal documents containing information about the type of product being shipped, the quantity of the product, and its destination.
Purge Certificate
If the engine or APU has been drained or purged, a purge certificate will be attached to the container. This certifies that the shipment is not DG or HAZMAT.
Why Have Shipping Insurance for an Aircraft Engine or APU?
Even with the proper precautions, engine and APU shipments may be damaged in transit. Investing in shipping insurance – and possibly a tracking device – for engines, APUs, and other high-value or fragile aircraft parts may be worth the extra expense. Some shipping companies or suppliers may offer a tracking device that can provide real-time updates about the shipment’s location, temperature, humidity, and other conditions during transit.
A damaged engine or APU could be costly for both the shipper and receiver. Damages incurred during delivery to a repair station or as a core to a supplier may result in extensive repair or overhaul and significantly higher costs than the initial quoted price – provided it is not beyond economical repair (BER). If an engine or APU core is BER, the shipper will need to either send another core in its place or pay the full price of the exchange unit.
Why Choose a Logistics Partner?
Logistics partners are third-party companies that handle the storage, delivery, and often the responsibility of their customers’ shipments. When shipping an aircraft engine or APU, consider working with a trusted logistics partner. This could be your preferred freight forwarder, engine repair facility, or engine manufacturer.
Aircraft Engine or APU Shipment Advice
From acquiring the right mount and shipping container to filling out the transport document, shipping aircraft engines and APUs takes time. If you are returning a core, the supplier will likely specify a due date for when the core is expected at their warehouse. Our advice is to schedule your time and plan ahead whenever possible to mitigate delays while ensuring your engine or APU is properly packaged and delivered safely.